Recycling von Kunststoffen – Eine Notwendigkeit
Vor dem Hintergrund verschmutzter Weltmeere (Mikroplastik) und dem zunehmenden Ressourcenverbrauch in allen Teilen der Erde bei gleichzeitiger Endlichkeit der natürlichen Ressourcen, gewinnen Ressourceneffizienz und Kreislaufwirtschaft in der heutigen Zeit an Bedeutung. Sowohl in Politik und Industrie als auch innerhalb der Gesellschaft findet ein Umdenken bezüglich eines nachhaltigen Umgangs mit den Ressourcen statt. Dies entwickelt sich zunehmend zur Kernaufgabe des 21. Jahrhunderts.
Wir am KTP sind uns der Verantwortung bewusst und nehmen uns der Aufgabe an.
Verwertung von Kunststoffabfällen in Deutschland
Bisher werden mehr als die Hälfte der Kunststoffabfälle thermisch verwertet, dabei ist sowohl das werkstoffliche Recycling als auch das rohstoffliche Recycling laut Kreislaufwirtschaftsgesetz vorzuziehen. Denn mit jeder Wiederverwertung steigt der ökologische Nutzen des Produktes an.
Zu den nachfolgenden Themen haben wir für Sie zusätzliche Informationen bereitgestellt:
Im Zuge des Forschungsprojektes wurde eine innovative Rückstaulängenreglung zur Vermeidung von Prozessschwankungen in Thermoformextrudern mit hohem Recyclinganteil entwickelt. Ein Teilprojektziel umfasste hierbei die Entwicklung eines Soft-Sensors, der als Kernstück für die Rückstaulängenregelung eingesetzt wird und diese entsprechend im Prozess detektieren kann. Die Rückstaulänge, auch Fülllänge genannt, stellt sich bei Extrusionsprozessen mit Entgasungszone ein. Letztere wird zur Entweichung flüchtiger Bestandteile (z.B.: Wasserdämpfe, Restmonomere und andere flüchtige Verunreinigungen), wie es beispielsweise bei häufig noch bedruckten Recyclingmaterialien der Fall ist, benötigt. Um die flüchtigen Bestandteile entweichen zu lassen, muss die Schnecke an dieser Stelle teilgefüllt sein, was durch eine Staustufe mit sprunghafter Vergrößerung des Kanalvolumens erreicht wird. Die sich einstellende Rückstaulänge ist insbesondere vom Gegendruck, der durch die Druckströmung des Werkzeuges induziert wird, und vom Rezyklatanteil des zu verarbeitenden Materials abhängig.
Weiterführend wurde im Projekt die Einzugsgeometrie des schnelllaufenden Extruders optimiert, sodass Mahlgüter, die zu Brückenbildung neigen, konstanter im Feststoffbereich gefördert werden können und sich entsprechend höhere Durchsätze erzielen lassen. Zudem wurde als weiteres Teilprojektziel die Entgasungsleistung durch Optimierung der Entgasungsöffnung verbessert, um höheren Anforderungen an qualitativ hochwertige Recyclingprodukte gerecht werden zu können.
Genauer Informationen zu diesem Projekt finden Sie hier: Projektbericht
Das Ziel dieses Projektes ist die Entwicklung einer Anlage zur direkten Verarbeitung von rezyklierten Kunststoffflakes. Durch den Einsatz dieser Technologie soll, neben der Erhöhung der Recyclingquote, die Qualität des rezyklierten Endproduktes gesteigert werden, um letztlich Produkte mit hohen Qualitätsanforderungen vollständig aus rezykliertem Material herstellen zu können. Hierbei wird das Rezyklat als Ausgangsstoff in Form von sogenannten Flakes (zerkleinerte Kunststoffteile) in einem Agglomerationsschritt zunächst zu fingergroßen Agglomeraten geformt. In einem Agglomerator verdichtet eine Zuführschnecke die Kunststoffflakes und fördert sie zwischen das Scheibenpaar des Agglomerators. Letzteres setzt sich aus einer Rotorscheibe, welche eine Rotationsbewegung ausführt, und einer Statorscheibe, welche als Gegenelement dient und nicht rotiert, zusammen. Durch das Kneten und Rollen der Kunststoffflakes zwischen den Scheiben entsteht Friktionswärme, welche das Material plastifiziert, ansintert und verdichtet. Hierbei wird im Gegensatz zur Extrusion der Schmelzpunkt des Materials nicht erreicht, da es nur in einen pastösen Zustand gebracht wird. Das Vorhaben hat zum Ziel, das Scheibenpaar des Agglomerators derart zu entwickeln, dass eine definierte und konstante Agglomeratgröße realisiert wird und diese Agglomerate auf direktem Wege einem Einschneckenextruder zugeführt und sofort zu einem Produkt verarbeitet werden können.
Genauer Informationen zu diesem Projekt finden Sie hier: Projektbericht
Eine große Herausforderung bei dem mechanischen Recycling von faserverstärkten End-of-Life Produkten ist der bei der Zerkleinerung entstehende Faserstaub. Dieser besteht aus potenziell lungengängigen Faserbruchstücken, welche ebenfalls WHO-Faser-Charakteristik aufweisen können. Als WHO-Fasern werden Fasern mit einem Durchmesser <3 µm, einer Länge >5 µm und einem Länge-zu-Durchmesser-Verhältnis von >3:1 bezeichnet. Sie können durch ein Zerspleißen von Glas- oder Carbonfasern bei mechanischer Beanspruchung entstehen und können potentiell toxisch sein. Das Ziel des Forschungsprojektes war es daher die Entstehung von WHO-Fasern oder alveolengängiger Staubfraktionen bei dem mechanischen Recyceln thermoplastisch faserverstärkter Kunststoffe zu untersuchen sowie deren Toxizität zu analysieren. Weiterhin sollte durch eine gezielte Optimierung der Parameter beim Zerkleinerungsprozess die Entstehung alveolengängiger Stäube verringert werden.
Untersuchungen an der Schneidmühle und am Einwellenzerkleinerer haben eine Zunahme der lungengängigen Faserstaubfraktion mit zunehmender Rotordrehzahl feststellen können, ebenso wie mit abnehmender Siebmaschenweite. Auch wenn insbesondere für die carbonfaserverstärkten Organobleche eine teils grenzwertüberschreitende Konzentration an alveolengängigen Faserbruchstücken gemessen werden konnte, wurde keine toxische Wirkung ermittelt.
Genauer Informationen zu diesem Projekt finden Sie hier: Projektbericht
In Anwendungsfällen, die besondere Materialeigenschaften erfordern, welche von Standardkunststoffen nicht erfüllt werden können, kommen technische Kunststoffe zum Einsatz. Häufig zeichnen sich technische Kunststoffe im Vergleich zu Standardkunststoffen durch bessere mechanische Eigenschaften aus. Es können aber auch andere Charakteristiken dafür entscheidend sein, dass diese anstatt eines Standardkunststoffs eingesetzt werden. Mit den besonderen Eigenschaften der technischen Kunststoffe geht ein erhöhter Materialpreis einher. Diese Wertigkeit technischer Kunststoffe ist ein Grund, die Materialien einer Wiederverwertung zuzuführen. Darüber hinaus vermeidet ein Recycling Kunststoffabfall und die energieintensive Herstellung von Neuware.
In diesem Forschungsprojekt sollen technische Kunststoffe wiederverwertet werden, indem aus den Kunststoffen faserverstärkte Compounds hergestellt werden. Die Compounds sollen dabei annährend die Eigenschaften von Compounds aus Neuware erzielen, sodass sie auch in anspruchsvollen Anwendungen zum Einsatz kommen können.
Die Compoundentwicklung findet auf gleichläufigen Doppelschneckenextrudern statt. Diese besitzen eine hohe Mischwirkung und eignen sich daher besonders für die Einarbeitung der Fasern in die Kunststoffschmelze.
Dadurch, dass die wiederzuverwenden Kunststoffe mit Zuschlagsstoffen versetzt sind, die bei der ursprünglichen Anwendung von Vorteil waren und bei Kunststoffabfällen keine Sortenreinheit garantiert ist, ergeben sich zwei Herausforderungen, die bei der Compoundherstellung aus Neuware nicht bestehen. Zum einen sind Mischungen aus verschiedenen Kunststoffen und Zuschlagsstoffen schwerer zu verarbeiten als fest definierte Rezepturen aus Neuware und bekannten Additivmischungen. Zum anderen können in den verwendeten Abfällen Kunststoffe enthalten sein, die zueinander inkompatibel sind. Diese Schwierigkeiten müssen bei der Materialentwicklung berücksichtigt und durch die Verwendung von Additiven bewältigt werden.
Genauer Informationen zu diesem Projekt finden Sie hier: Projektbericht
Werkstoffliches…
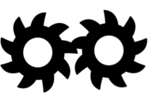
Rohstoffliches…
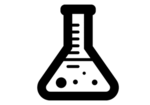
Thermische Verwertung
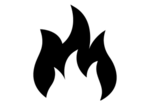
Deponie
