Research
Plastics are becoming increasingly important in modern mechanical engineering and are displacing traditional materials such as wood, metal and glass from their areas of application.
The Plastics Technology Paderborn (KTP) is divided into two groups:
"Plastics Technology", led by Prof. Dr. Ing Elmar Moritzer, focuses on the analysis of manufacturing processes in injection moulding technology, composite technology and joining technology for plastics, as well as the recycling of plastics production waste.
The "Plastics Processing" department, headed by Prof. Dr. Volker Schöppner, is involved in research and development of manufacturing processes. The knowledge gained is used to gain a better understanding of processes, which is offered to industry in the form of user software.
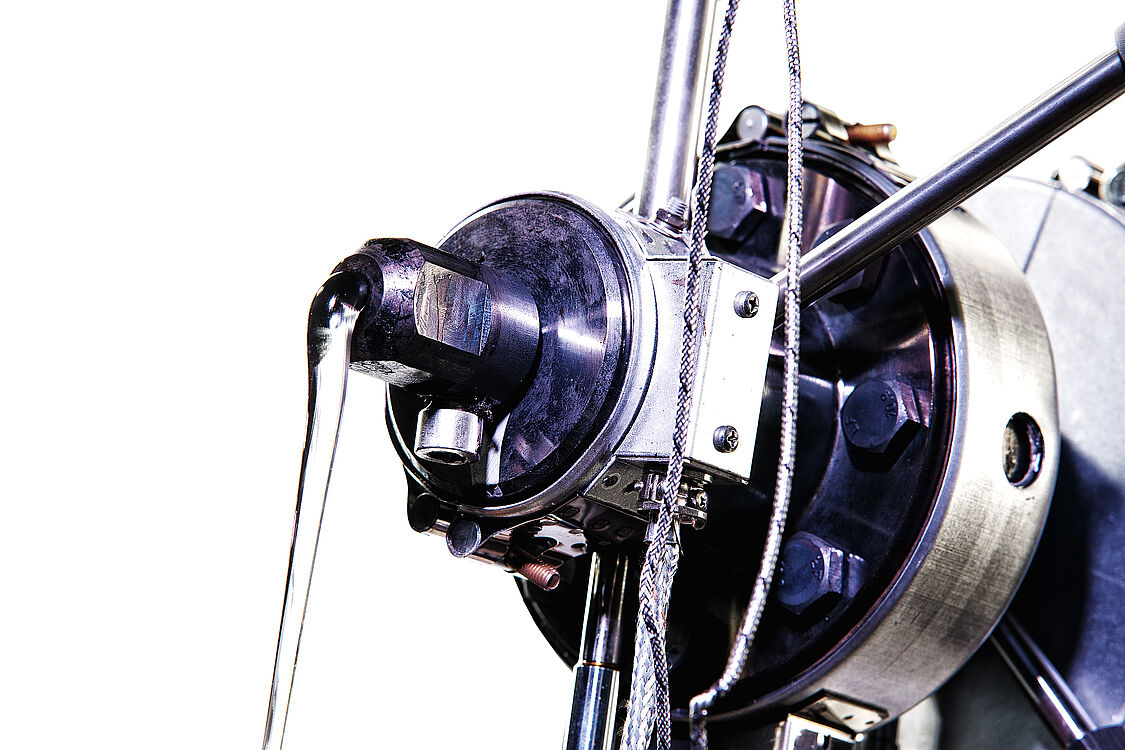
Extrusion
The plastics processing method of extrusion is represented in different versions at KTP. We have access to an extensive range of machinery consisting of a portfolio of different extruders and downstream equipment from numerous manufacturers. Our areas of activity range from general process and procedure design to detailed component and product design. The"REX" software for single-screw extruders, for example, is used for this purpose.
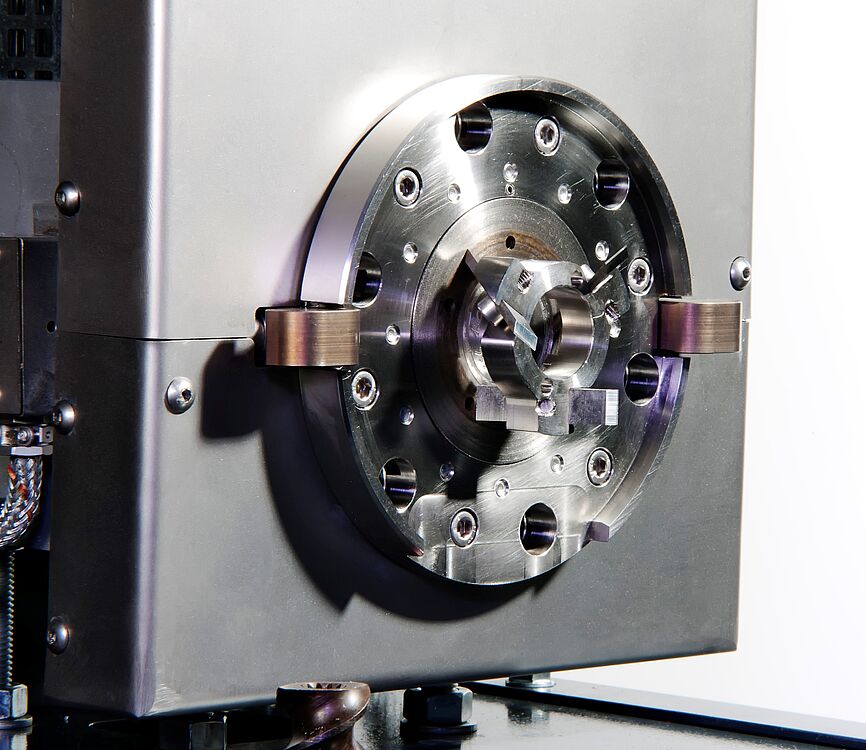
Compounding
The plastics processing method of compounding is also represented at KTP. It has access to an extensive range of machinery consisting of a portfolio of various co-rotating twin-screw extruders and downstream equipment from numerous manufacturers. It is possible to mix in supercritical gases, additivate them and then granulate them in both cold and hot die casting. Our fields of activity range from general process and process engineering to detailed component and product design. The"SIGMA" software for twin-screw extruders, for example, is used for this purpose.
Injection moulding
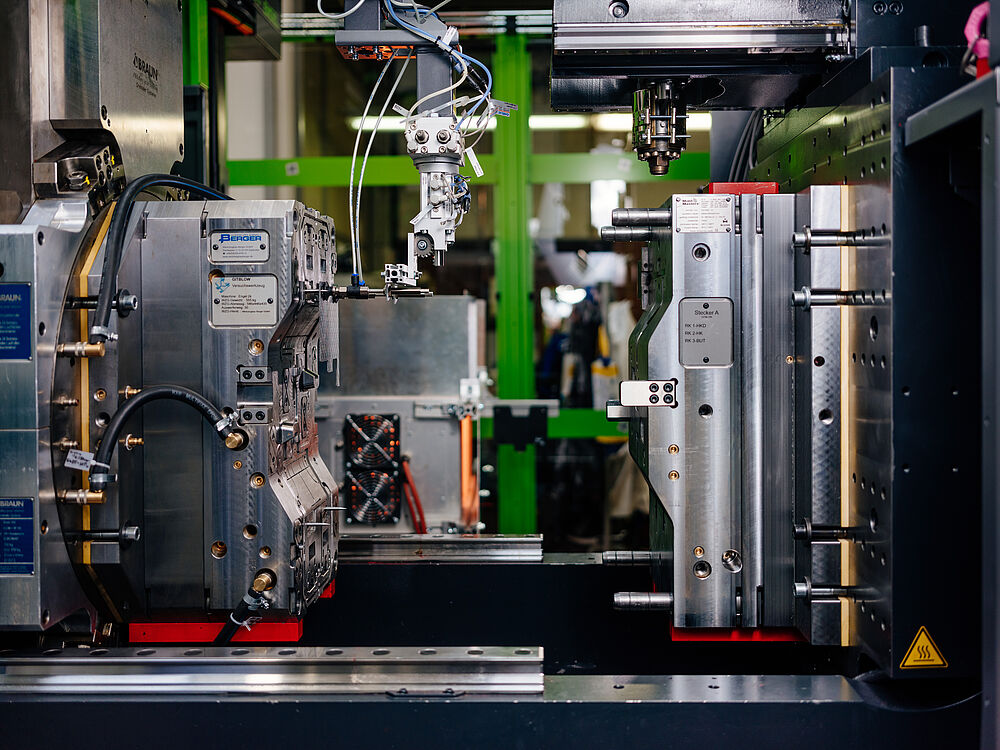
Kunststofftechnik Paderborn has been involved in injection moulding, which alongside extrusion is the most widely used plastics processing method, since its foundation. In addition to the conventional 1-component injection moulding process, research is being conducted into the special injection moulding processes of 2-component composite injection moulding, sandwich injection moulding, gas injection technology (GIT) and the GITBlow process developed at KTP. In addition to the process technology of injection moulding, our areas of activity also focus on filling behaviour in the mould and on mould technology.
Additive manufacturing processes
Together with other chairs in the Faculty of Mechanical Engineering, Paderborn Plastics Technology is an integral part of the Direct Manufacturing Research Centre (DMRC). The DMRC focuses on additive manufacturing processes that are used to produce components, known as direct manufacturing, and represent an important technology of the future. This new type of manufacturing promises significant advantages over conventional processes, such as reduced production and process costs, shorter throughput times, more complex component geometries or the demand-orientated production of components and spare parts. The aim of the DMRC is to further develop additive manufacturing processes and the components produced in this way until they are ready for series production.
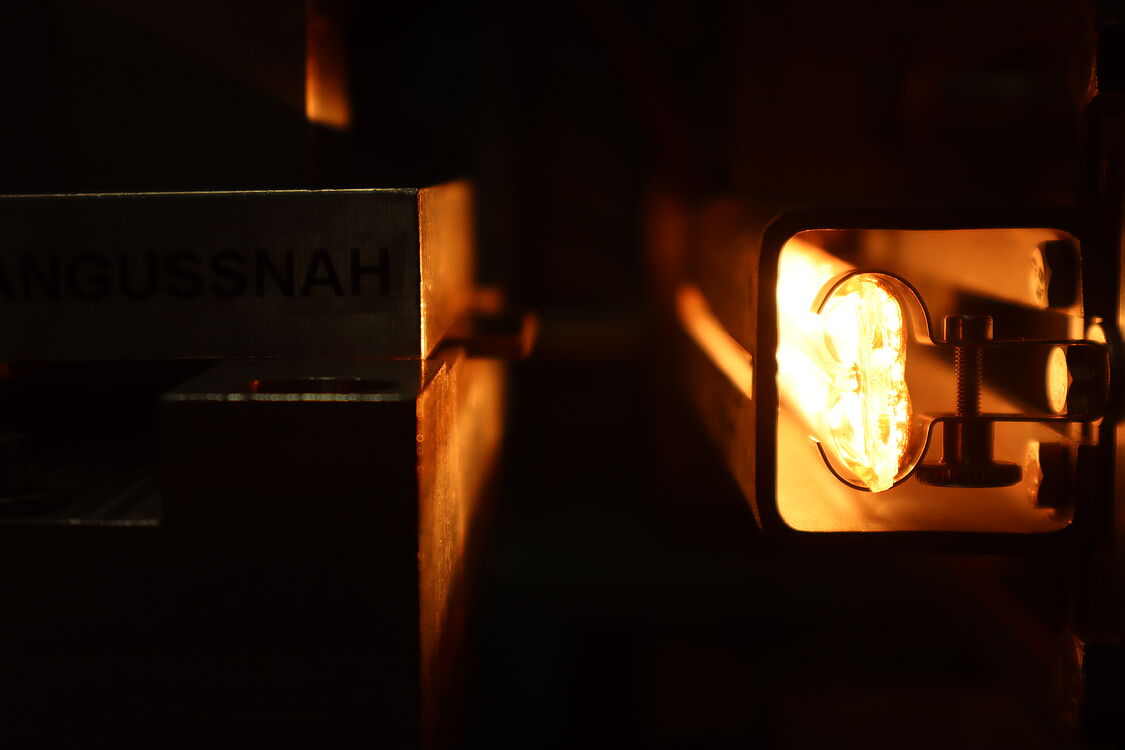
Joining technology
The welding of plastics and mechanical joining technology are an integral part of Kunststofftechnik Paderborn. The in-house joining laboratory deals with a wide range of problems in the field of established welding processes, such as hot plate, vibration and laser welding, as well as special processes such as microwave or high-frequency welding. Bonded joints with plasma pre-treatment as well as mechanical joining processes, such as direct screwing and self-pierce riveting, can also be realised here, and a comprehensive analysis of the joints can be carried out in the test laboratory using various evaluation methods based on the latest techniques.
Nachhaltigkeit & Kreislaufwirtschaft
Die Transformation zu einer nachhaltigen und ressourceneffizienten Kunststoffwirtschaft stellt eine zentrale Herausforderung unserer Zeit dar. An der Kunststofftechnik Paderborn (KTP) arbeiten wir daran, Lösungen dafür wissenschaftlich fundiert und praxisnah mitzugestalten.
Ein Schwerpunkt unserer Forschung liegt auf den sogenannten R-Strategien der Kreislaufwirtschaft: Reduce, Reuse, Repair sowie verschiedene Recycling-Ansätze - mechanisch und chemisch. Diese Prinzipien bilden die Grundlage für eine Vielzahl an Projekten, in denen wir innovative Technologien, Werkstoffkreisläufe und Anwendungsszenarien erforschen.
Neben unserer Grundlagenforschung realisieren wir anwendungsorientierte Kooperationsprojekte mit Industriepartnern, bieten wissenschaftliche Dienstleistungen, Analysen sowie Schulungen zu nachhaltigkeitsbezogenen Themen an.